(The race for extreme ultraviolet lithography,
part 2)
Meanwhile, back at the beamline...
A second set of mirrors designed for use in Sandia's ETS was of much higher
quality. Because these were not immediately needed in the ETS, Naulleau
and Goldberg and their colleagues modified the at-wavelength interferometer
and used it to print test patterns.
"The interferometer is wonderful for testing optics, but the proof
of what the optics can do is in the printing," says CXRO's present
director, Erik Anderson. He explains that "because high-coherence
ALS light is ideal for interferometry but not for printing, Paul Denham
and Patrick Naulleau developed a scanning illumination system that could
fill the patterned mask area with a wide, programmable range of incident-angle
EUV light. Using this scanning illuminator, we can produce almost any
possible illumination pattern, which is very important in lithography
research."
The resulting device was called the SES, the "static exposure station"
-- static because, unlike the full-blown ETS, it projects only a portion
of a mask pattern and exposes only part of a wafer at a time.
|
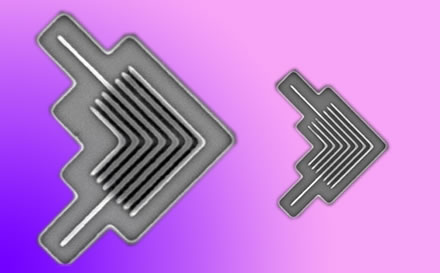 |
|
With optics designed for 100 nm features,
the subfield exposure station easily created 70 nm features, as in
these "elbows" (left). Exposure process control enabled
printing of 39 nm features (right). |
|
The actual chip-making performance of the optics was even better than
they had been designed to achieve. Mirrors designed to make features with
better than 100 nanometer resolution readily created 70 nm features. And
by manipulating parameters like beam angles and exposure times, the CXRO
team achieved much smaller features spaced just 39 nanometers apart.
They also tested ways to get rid of defects in masks. "If there's
a defect at the bottom of all those layers, you can't directly repair
it. So the question is how to smooth it out." The team used the Nanowriter,
CXRO's ultra-high-resolution electron-beam lithography machine, whose
operations Anderson manages, to create masks with programmed defects.
With the SES, they printed from these masks using different coatings
developed at Livermore. Anderson says, "Coatings optimized for smoothing
minimized the irregularities, like snow on grass. With nonsmooth coatings,
the defects stood out like snow on a boulder."
|
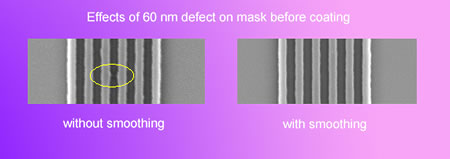 |
|
Programmed defects were introduced
into masks before coating. Coatings optimized for smoothing reduced
irregularities in printed features. |
|
By printing from the newest set of optics and special test masks, says
Anderson, "we have verified the interferometry and demonstrated the
impressive capabilities of EUV lithography."
And as commercial chip manufacture draws closer, CXRO's EUV interferometer
has another role to play. "We set the standard in interferometry,
but for commercial use, the goal is get visible-light interferometry accurate
enough so that at-wavelength interferometry won't be needed for EUV steppers
used in routine manufacturer. In close collaboration with our partners
at Livermore, who specialize in visible interferometry, our task is to
help insure that the required accuracy is achieved."
The size of things to come
In April of 2002, Intel ordered the first "beta" EUV stepper
from the experienced, Netherlands-based lithography manufacturer ASML,
to be delivered in 2005.
Meanwhile current photolithography techniques, which have already used
deep ultraviolet light at 248 nm wavelengths to craft chips with line
widths of only 80 or 90 nanometers, will be extended to 193 nm and possibly
157 nm wavelengths for making chips with line widths less than 70 nanometers.
To make anything smaller than that, EUVL is essential. By 2007, commercial
production of chips at the 45 nm "node" is expected to begin,
using Intel's ASML beta machine. By 2009, capability will be extended
to the 32 nm node, resulting in finished chips with 13 nm line widths
or less.
Computers using the first EUVL-made chips are expected to have ten times
the speed and ten times the memory of today's machines. That will be just
the beginning of the next generation of superdense integrated circuits.
Additional information:
Back to part 1
|