Deb Hopkins with Lawrence Berkeley National
Laboratory's Engineering Division wanted to build a car with a body made
of lightweight composite materials and a quality-performance internal
combustion engine that would get about 80 miles to a gallon of gas. She
didn’t get the money for that, but she did get the funding to
investigate the nondestructive evaluation (NDE) techniques that will be
needed if such vehicles are to ever become a commercial reality.
"Lightweight composite materials must be adhesively bonded which
means the tear-down safety inspections of spot-welded steel structures can’t
be used on them," says Hopkins, now in her fourth year on this
research which is funded under the Partnership for a New Generation of
Vehicles, a collaboration between the federal government and the U.S.
Council for Automotive Research.
THE IR THERMOGRAPHY SETUP AT TOP AND THE TWO SETS OF DATA
BELOW SHOW HOW THE TECHNIQUE CAN IDENTIFY GOOD SPOT WELDS,
DIFFERENTIATING FROM POOR ONES. AFTER THE RAW DATA (A) IS
PROCESSED, THE SECOND SET OF DATA (B) SHOW TWO HIGH-STRENGTH SPOT
WELDS ON THE OUTSIDE AND THREE LOW-STRENGTH WELDS IN THE MIDDLE.
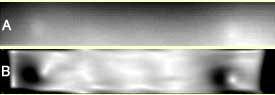
|
Even for conventional welding, the tear-down method of testing, in
which the structural components of a vehicle are literally torn down to
assess the integrity of their welds, could stand improvement, Hopkins
says. In a typical U.S. automobile manufacturing plant today, production
components are pulled off assembly line at regular intervals for a
tear-down inspection. Not only is this a time-consuming and costly
procedure, it is also only a statistical sampling and not an inspection of
every component that is manufactured.
"On-line nondestructive evaluation techniques offer the promise of
testing 100 percent of all production components in real-time with the
ability to spot problems immediately," Hopkins says. "It is also
the only way to ensure the integrity of adhesive-bonded joints in
lightweight composites."
In addition to monitoring product quality, on-line NDE can also be used
to monitor the production process and identify areas in which the process
can be improved.
Says Hopkins, "With on-line NDE, the automobile industry should be
able to improve production efficiency and reduce waste."
For use in an automobile manufacturing plant, NDE techniques have to be
able to reliably operate under hot, dusty, and noisy conditions.
Diagnostics must also be performed quickly and accurately. Hopkins and her
colleagues in the Engineering Division have been working to develop NDE
sensors and data processing and modeling tools. To date they’ve
experimented with a wide range of NDE methods including acoustics and
infrared thermography.
The acoustic NDE techniques being examined entail exciting a component
with a transducer which converts electrical pulses into mechanical stress
waves, then analyzing the elastic waves -- body, surface, or standing --
that are generated. With body and surface waves, test results are derived
from wave attenuation, frequency content, and velocity. With standing
waves, resonance is analyzed to measure frequency response, mode shapes,
and damping characteristics.
"It is well established that these waves are sensitive to the
presence of flaws, voids, cracks, heterogeneities, or some other change in
material properties," says Hopkins. "For example, a crack will
reflect some of the wave energy, slow and attenuate the wave, and change
the resonance properties of the component being tested."
Hopkins and her group have been using a steel-frame rail as a model for
associating their measurements with specific characteristics of spot
welds. The success of any NDE technique in the automobile industry depends
upon its ability to quickly and accurately distinguish between critical
defects that affect the structural integrity of a component and defects in
low stress areas that would not significantly affect the component’s
stiffness or strength.
"Cycle times in the auto industry typically run about 15 to 20
seconds and the data acquisition and analysis of an on-line real-time NDE
must be fast enough to render a go/no-go decision within this
timeframe," says Hopkins. "That’s the major challenge for the
use of NDE techniques in automobile manufacturing."
With acoustic-based NDE techniques, the tradeoff, according to Hopkins,
is between speed and resolution.
"If you have the time and access to the components, you can make
highly detailed measurements with acoustic techniques," she says.
"The faster we can learn to acquire and interpret data the better our
measurements will be."
Infrared (IR) thermography offers speed and high resolution plus the
advantage of full-field imaging. Measurements for this NDE technique are
derived from changes in thermal resistance that arise in the flow of heat
through the components. These changes can be detected by IR cameras that
are sensitive to surface temperature differences of less than 0.1 degrees
Celsius.
"IR thermography can be used to characterize defects in welds and
voids in materials such as gaps in adhesive layers or air bubbles,"
says Hopkins. "These defects and voids have a much higher thermal
resistance than the surrounding material."
To utilize IR thermography, a heat flow must first be established
through the components to be tested. This is done by heating one side of
the component while the opposite side is cooled. The resolution obtained
through IR thermography depends upon the thickness and thermal
conductivity of the material being tested but Hopkins says the technique
is applicable to a wide range of lightweight composites.
The use of more lightweight metals (aluminum and magnesium) and
composite materials in place of steel in the components of automobile
bodies could reduce overall vehicle weight by 40 percent or more and make
the dream of 80 miles per gallon of gasoline an industry standard.
Says Hopkins, "We’ve proven that acoustic and IR thermography
NDE techniques work well in a laboratory setting. The next step is to show
that they can be made to work equally well in a factory setting."
Working with Hopkins on this project are the Engineering Division’s
Daniel Turler and Murat Karaca, plus Seiji Nakagawa and Kurt Nihei of
Berkeley Lab’s Earth Sciences Division.
Additional information:
|